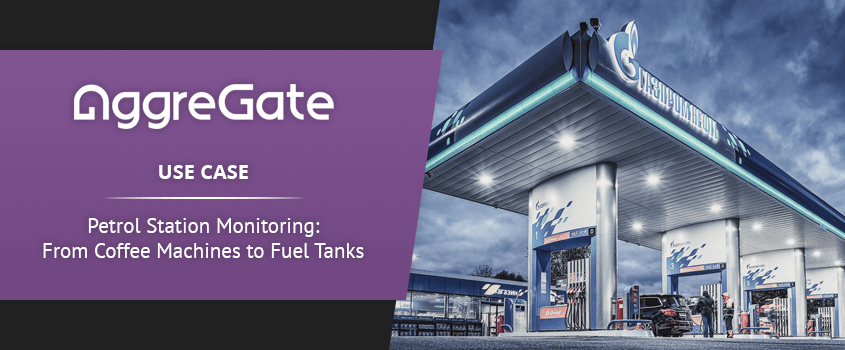
We continue sharing interesting projects built on the basis of AggreGate IoT Platform. Today we’re referring to the monitoring of the Gazprom Neft petrol station chain. We’ll cover the main issues and tasks of the customer as well as their solution and results.
What’s the Problem?
So, the Gazprom Neft company required to arrange complex operation control over all their petrol stations implying:
- monitoring of commercial and network equipment, tank terminals, fuel dispensers and price boards.
- device data collection, visualization, profound analytics.
- possibility of distant service unification, remote diagnostics, and repair.
Before the solution implementation, the customer had to face a number of problems at sites:
- Troubles could be diagnosed only during periodic maintenance that is not more often than once a month.
- Fuel dispenser problems (for example, lower filling speed due to a filter blockage or any other malfunction) would normally cause its shut down for repairs for about 5 hours. It’s easy to figure out that even 5 hours daily shutdowns result in significant financial losses.
- It was impossible to monitor trading and cash equipment or to control the quality of both the main product (fuel) and associated goods (coffee, for instance).
That is how the Infrastructure Monitoring Center (IMC) project appeared, and AggreGate IoT platform became its software basis.
Why AggreGate?
The choice in favor of AggreGate IoT Platform was made mainly because of its flexibility and wide possibilities for integration and further functional development. Besides, AggreGate ownership cost is optimal as compared to analogs in the market.
How to Solve? What’s the Result?
As a result, the IMC project was launched in 2017, and Gazprom Neft has implemented self-service cafes at petrol stations by connecting all the coffee machines to a unified intelligent system managing coffee sales. The following benefits were achieved:
✅ Equipment complex operation control and possibility of remote repair.
✅ Remote setting of a unified recipe and high quality of coffee making throughout the petrol station chain.
✅ Consequently, record-high coffee sales at petrol stations.
After that, the company decided to connect all the petrol station equipment and systems to IMC. More than 1500 petrol stations all over Russia have been connected.
After the monitoring center was launched, station equipment stays in working condition 99% of the time and technological downtime decreased by 30%.
As for fuel dispensers malfunction detection, IMC automatically registers filling speed reduction and instantly notifies the service company.
A new intelligent system streamlines the workflow and improves the efficiency of each petrol station in the chain.
Instead of a Conclusion
“Connecting our petrol stations to the Internet of things is an important step on the way to the growth of business efficiency and transparency. We managed to significantly cut equipment maintenance costs and provide highest-level control over oil products quality and quantity having excluded human factor from the process. It means, our clients can be sure to get a high quality product exactly in the required quantity.”
![]() |
Alexander Krylov - Regional Sales Director, Gazprom Neft |
You can find out more about this use case in the catalog and address your questions to our sales team. 🙂